Numerous machining techniques are employed by industrial mechanical firms to create items out of various materials. Mechanical CNC turning service is among the most used machining processes.
The term “turning” is commonly used in the industry to refer to a process that forms the basis of mechanical technology and has led to modern machining. In essence, the CNC turning service involves rotating the workpiece in the opposite direction of a cutting tool. Round bar stock is primarily utilized for machining products.
In industrial machining, turning is commonly employed as a technique to improve or incorporate additional characteristics into pre-existing pieces. This method often results in a highly polished surface and offers precise outcomes.
This article delves into the intricacies of three critical types of turning in machining.
Rough Turning
Roughing in machining refers to the process of removing a substantial amount of excess material from workpieces. This initial step is commonly undertaken in mechanical engineering for further processing. CNC rough turning, in particular, is capable of producing a material shape or form that closely matches the desired component geometry. This not only simplifies future machining operations but also improves their efficiency.
There are numerous distinct advantages to be gained from delving into the realm of rough turning.
- The most notable advantage of rough turning is the exceptional speed at which it removes bulk material. This technique effectively eliminates excess material, streamlining the machining process and enhancing productivity.
- To prolong the lifespan of delicate final equipment, it is crucial to engage in rough turning. By effectively eliminating the majority of the material, rough turning diminishes the stress and wear experienced by finishing tools, thereby enhancing their operational longevity.
- Roughing operations help to bring the workpiece closer to its final shape, significantly minimizing the time required for subsequent machining steps. This enhanced efficiency can lead to shorter manufacturing cycles and potentially lower costs for the final product.
Semi-Finish Turning
Semi-finishing is a crucial service in the manufacturing industry, where a product is brought to a specific level of completion before the final finishing stage. This process is essential to ensure that the end product meets all the necessary standards and requirements. Semi-finish turning involves eliminating any imperfections on the product’s surface through techniques such as sanding, polishing, and grinding. To achieve the desired level of precision and smoothness, specific tools and equipment are employed during the operation.
Semi-finish turning, also known as intermediate or midway turning, plays a vital role in factory construction. These techniques for semi-precision turning bring numerous advantages and are crucial in transforming raw materials into finished products.
We will analyze the significance of semi-finish turning in facilitating efficient and cost-effective production processes.
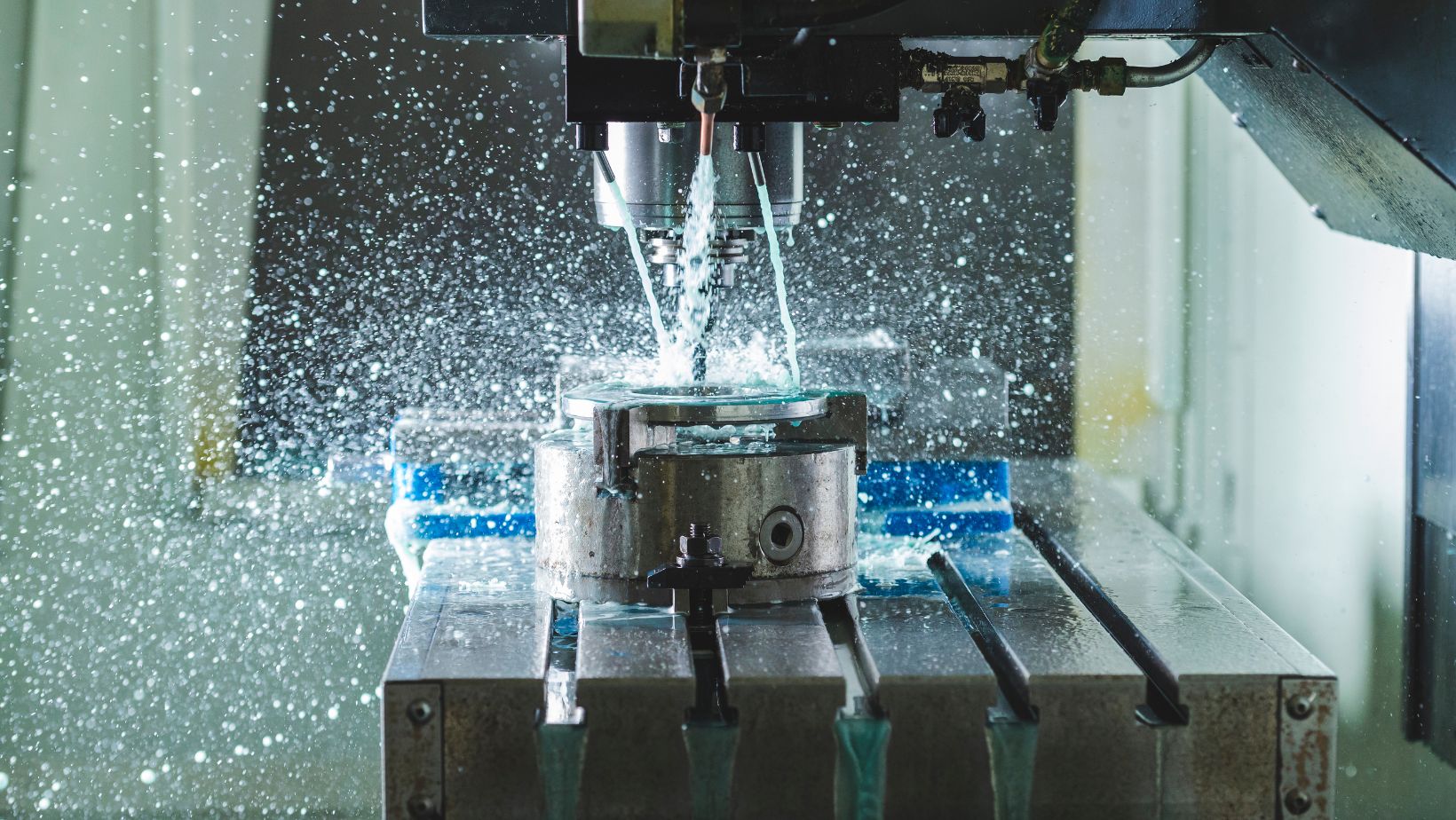
- Partially processing materials through semi-finish turning significantly reduces production costs. Manufacturers can effectively cut down on manufacturing expenses, saving valuable time and money. This approach ensures enhanced machining capabilities that are not only cost-effective but also contribute to increased profitability.
- Integrating semi-finished items, especially during mid-stage machining, enhances efficiency. By focusing on product completion and refinement instead of starting from scratch, businesses can expedite the production cycle.
- The process of semi-finishing offers enhanced versatility to the production process. These materials allow manufacturers to readily adapt to evolving consumer preferences and market dynamics by being easily tailored for various end products. This adaptability during machining proves to be a valuable asset in today’s fast-paced business environment.
- Semi-finish turning is a vital stage in the production process due to its ability to enhance the quality and aesthetics of the final product. By ensuring flawlessness and visual appeal, it plays a crucial role in delivering a superior end result. Additionally, as the product has already undergone substantial refinement at this stage, semi-finishing significantly reduces the time and cost required for the final finishing phase.
Finish Turning
CNC finishing, also known as finish turning, is the final step in the machining process. It follows rough and semi-finish turning and aims to achieve precise measurements, tight tolerances, and a superior surface finish, which are crucial for the end product.
In rough turning, the emphasis is on making strong, aggressive cuts, whereas finish turning involves using advanced equipment to make delicate, precise cuts. This crucial step meticulously smooths the surface of the part to ensure it perfectly aligns with the design specifications. The final touch adds a sleek, polished look to the product and guarantees the precision necessary for optimal performance.
Advantages of Semi-Finish Turning:
- The significance of this component is emphasized through its meticulous attention to detail and flawless finishing, creating a perfect balance between operational efficiency and visual attractiveness.
- Hence, companies utilize a tailored finish turning technique or a suitable combination of finishing steps to enhance or incorporate desired characteristics in the manufactured components, such as enhanced adhesion, corrosion resistance, electrical conductivity, solderability, hardness, wear resistance, and more.
- The final stage in CNC production projects is generally known as finish turning. This stage is performed after the engineer has completed the initial roughing processes on the workpieces. The purpose of finish turning is to finalize the construction of the component by removing any excess material and achieving the desired final parameters in terms of thickness, tolerances, roughness, flatness, and surface finish.
Correct Turning Process
No company desires to witness the destruction or wastage of the product after CNC turning has been completed. Furthermore, there are various factors to consider before reaching the finishing stage. However, employing the right tools and adopting an appropriate approach can aid in maintaining work within budget and on schedule. The following measures will assist you in attaining the finest surface finish possible:
Quicken Your Pace
This holds particularly true when using carbide tools. Along with reducing the contact time between the material and the tool tip, enhancing the surface feet per minute speed (SFM) can also reduce the accumulation of edge buildup on the tool. This, in turn, prevents subpar surface finishes.
Cut Down on Your Feed Rate
By decreasing the feed rate, one can enhance the surface finish, resulting in increased longevity of the insert and reduced flank wear.
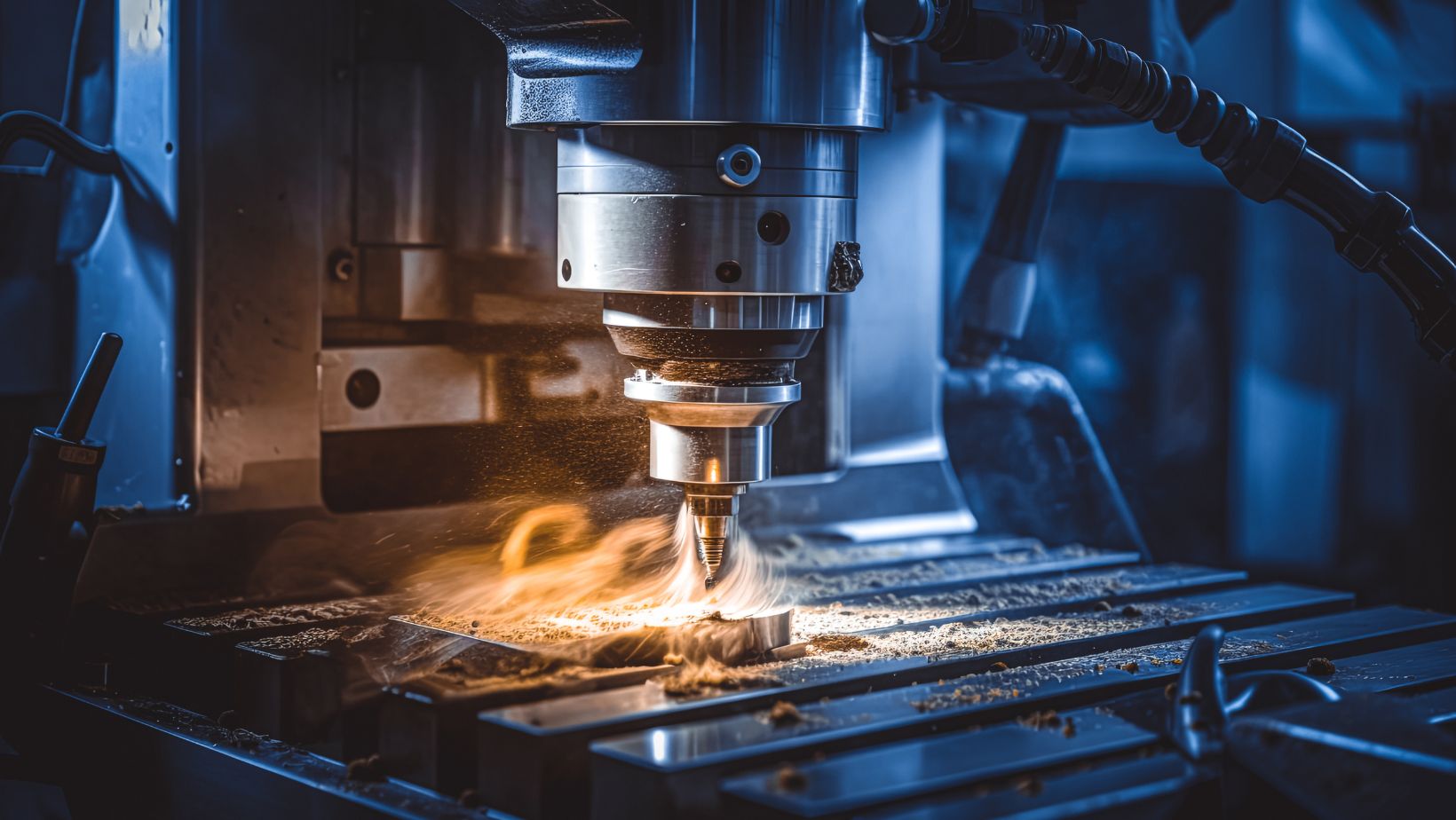
Increasing the nose radius by a factor of two will contribute to improving the smoothness of the surface. When dealing with roughing tasks, it is recommended to employ a tool that allows for a high feed rate, enabling efficient material removal. On the other hand, for finish turning, it is optimal to use a tool that delivers a finer cut and a reduced feed rate.
Raise the Angle of the Top Rake
Positive rake angles require lower cutting forces, resulting in a higher quality surface finish. When a 45° cutter is used, downward pressure on the part can cause it to flex, leading to an inferior surface finish. On the other hand, a 90° cutter will not bend the item but instead generate cutting forces parallel to it, resulting in a smoother surface finish.
Employ the Appropriate Method
To achieve a thick-to-thin chip, focus on creating a smooth surface finish. Your approach plays a crucial role in this. For a seamless transition between lines, opt for a cutter narrower than the nose radius.
Conclusion
In this article, we have witnessed the complexities involved in mechanical CNC turning. However, if your goal is to produce high-quality machined parts, familiarizing yourself with the three fundamental types of turning in machining is crucial.
Despite the numerous advantages of turning, there are also drawbacks such as tool wear and environmental issues. Consequently, various efforts are being made to enhance this method, ensuring safety, effectiveness, and feasibility as technology continues to advance.
Three Essential Types of Turning in Machining You Should Know